First, we recently switched some of the hard materials Third, we are actively researching novel alternatives the binder phase for percussion drilling applications used for saw blade applications from traditional to traditional tungsten carbide – cobalt (WC-Co) without the inclusion of cobalt, and 2) microstructural tungsten carbide – cobalt (WC-Co) hard metals to hard metals for percussion drilling applications in design for damage-tolerant components exposed to titanium carbonitride (TiCN)-based cermets. Not only collaboration with academic partner institutions. wear. Furthermore, our internal experts will play a key does this lead to a considerable reduction in the Several cobalt-free candidate materials emerged advisory role for other topics within the AIM-NEXT content of tungsten, cobalt and tantalum, but also to from a sponsored PhD project, which concluded in project in close collaboration with our research and a substantial performance improvement in terms of 2023, in partnership with the Technical University of industry partners. lifetime, considerably reducing the cost-per-cut for our Vienna. These materials are currently being re昀椀ned in customers. Our new line of X-Cut circular saw blades, collaboration with external suppliers and will soon enter for thin and structural metal cutting applications a testing and optimization phase. and launched in 2022, already bene昀椀ts from this substitution. We are investigating possible expansion Fourth, through our involvement in wider-scale R&D to other product lines. In addition, we kicked off R&D projects, which are jointly funded by public institutions, projects with academic partner institutions to develop by private companies and by industry consortia and custom cermets for our applications, thus further trade associations, we are supporting long-term, driving product differentiation and sustainable product cutting-edge scienti昀椀c research. The most recent design. development is our active involvement in the EU- and industry-funded “Accelerate the design and insertion Second, we are conducting an extensive internal of non-CRM hard materials for next generation project to reduce, or even obviate, the use of cobalt extreme applications”, or AIM-NEXT project. It will and nickel in our diamond inserts. We are investigating focus on establishing new experimental methods and the use of cobalt- and nickel-free metal matrix computational approaches for the design of tools composites and alternative thick coatings for these without CRMs, such as tungsten or cobalt, which are inserts, while ensuring that their best-in-class cutting currently essential for high-performance applications performance remains unchanged. This goes hand in like percussion drilling. This 4-year project will kick off hand with establishing reliable manufacturing process in 2024 and will fund ten researchers at institutions chains in collaboration with our plant engineering across the EU. Hilti will host two researchers as part colleagues. of AIM-NEXT, who will focus on 1) strengthening
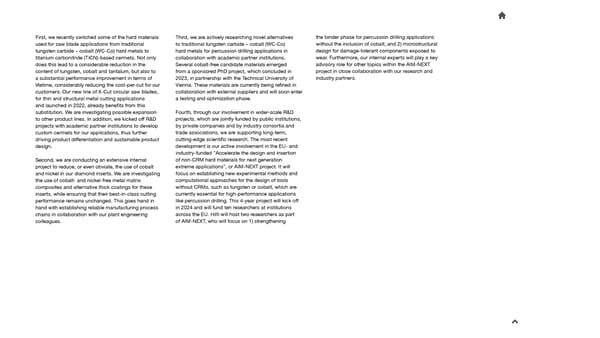